Camac Blog
The story of our soundboards
News
April 1, 2015
“Nothing is holier, nothing is more exemplary than a beautiful, strong tree. When a tree is cut down and reveals its naked death-wound to the sun, one can read its whole history in the luminous, inscribed disk of its trunk: in the rings of its years, its scars, all the struggle, all the suffering, all the sickness, all the happiness and prosperity stand truly written, the narrow years and the luxurious years, the attacks withstood, the storms endured. And every young farmboy knows that the hardest and noblest wood has the narrowest rings, that high on the mountains and in continuing danger the most indestructible, the strongest, the ideal trees grow.”
Hesse: Bäume. Betrachtungen und Gedichte
The soundboard is the soul of a harp. It transforms the vibration of the strings into sound. The frequencies it creates, amplified by the soundbox, define the sound quality. Having a new soundboard fitted is always a time of great anticipation for musicians, because it is akin to giving the instrument a new voice.
There is no better material for a harp soundboard than spruce, because of its high stiffness-to-weight ratio. Spruce can take a lot of tension, without having to be at the sort of thickness that would make it impossible to capture the string vibrations sensitively. For example, we taper our soundboards from 10mm in the bass register of a concert harp, to 2mm at the top – and there are over two tons of force pulling on this soundboard from the strings, so you can imagine how strong the wood, at best a centimeter thick, has to be.
We source our spruce in collaboration with Holzwerk Strunz, a family company at the foot of the Alps, that has specialized in tonewood spruce since 1820. Now headed by Thomas Hilz, they make the first expert cut of the spruce. It is their two hundred years of experience in painstaking selection and cutting that allows us to guarantee the quality of the wood.
Perfect soundboard spruce needs have dense, even rings – that is, it needs to come from mature trees, which have grown slowly over the course of two centuries. Trees grow more slowly in cooler temperatures, which is why altitude is so important. For our soundboards, we only consider wood that has grown at a minimum altitude of 1000m, and from forests that are members of the PEFC sustainable forests programme. “Austria has the oldest sustainability laws in the world”, says Thomas. “It has been the law for over three hundred years that you must plant more wood than you cut.”
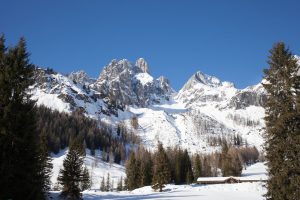
In the Alps, where the trees are chosen. The mountain in the background is called the “Bischofsmütze” or “Bishop’s hat”, because it looks like a Bishop’s hat. It is said to be a source of peculiar power and energy…
For every mature tree that is harvested, new ones are planted as part of the PEFC sustainability programme. In this part of Austria, trees are also only cut once the young trees are established and growing well, so that ground is never left bare.
After the logs have been selected on the mountainside, they are brought to the sawmills. It is a process that often requires patience – if there is too much snow, the logs have to stay on the mountain until the roads are passable again – and then, action! The logs need to be cut quickly because if they are left for too long in warmer temperatures, they will quickly start to develop black stains. This is not a problem for acoustic quality, but it is a cosmetic one.
Perfect soundboard spruce needs close-grained wood (sometimes so close, that you can barely see the rings), and this equates to the first 12-15cm from the bark of the log. “The middle is not suitable”, Thomas explains, “because young trees have a lot of knots in their wood, and of course those knots stay in the middle as the tree matures and thickens”. Once the first cut has been made, a second one quickly follows. Finally, one hundred logs will yield about two cubic metres of top quality soundboard material.
Following the first two cuts, the wood is dried in kilns for a long period, according to thickness. Soundboard wood has to be dry because if it isn’t, it will shrink over time. “If the spruce contains forty percent moisture when it is hewed, this will become twenty percent at sea level, and we dry it down further to six percent”, says Thomas. “We then use the wood that comes out of the kilns at exactly six percent.” This is the level we dry it to again in our own kilns, after it has gained some moisture in transport. Because drying is stressful for wood, if has been at six percent once already, it is much less likely that it will split on the second drying. For the same reason, the wood also has to rest both at Strunz and in Mouzeil for a minimum of three months, at a level of 7% humidity. This is an essential test of the wood’s stability.
Once the drying and resting has been completed at Strunz, there follows a third cutting to eliminate any remaining imperfections in the wood. Before it is delivered to Mouzeil, each cut is marked with the personal sign of the craftsman who did it, for the continuity and reliability of the quality control.
After the spruce has finished its second drying and resting in Mouzeil, the soundboard construction can finally begin! Firstly, we polish the outward facing side of the board, to prepare the surface for the veneer, and then we veneer it. After this, we taper the board, which is a particularly precise and delicate operation because the tapering must be absolutely even. Then we add the central string strip – a bar of hard wood – which holds the string eyelets.
Inside the soundbox, we then add the reinforcing bars, which have a big role to play in the soundboard’s solidity. We also apply the soundboard ribs, which make the board more rigid. Rigidity is important for sound quality and clarity, as well as for a long life for the harp.
The reinforcing measures are followed by joining all parts of the soundbox and board together – another very delicate operation, because this determines the positioning of the strings. Then, the harp can move on to the next stages in its long assembly.
Even when it is only a day out of our ateliers, the soul of a brand-new Camac harp is already two hundred years old.